Technologies
Indirect Dryer Units
The IQ Energy Indirect Dryer unit has been designed through decades of experience handling biomass feedstocks from the previous thermal treatment projects that the IQ Energy team worked on. The Indirect Dryer unit slowly dries out the dewatered waste input continuously moving it across serpentine belts with heat applied indirectly (the heat not contacting the product). This process significantly reduces the weight and volume of the waste input and dries it to a valuable product for agriculture, industry or as an input to the thermal treatment process. The Indirect Dryer unit typically takes a dewatered waste input of~80-85% moisture content and dries this down to an easy to handle ~15-20%moisture content.
Indirect Dryer - Inputs & Outputs
Indirect Dryer Input Examples

Biosolids/Sewage Sludge
Agricultural Wastes
Animal Wastes, e.g. Manures
Anaerobic Digestion Digestates
Mixed/Contaminated Organics, e.g. Food Organics
Mixed Residual Wastes
Other Wet Wastes
Dewatered Sludge (~80-85%MC)
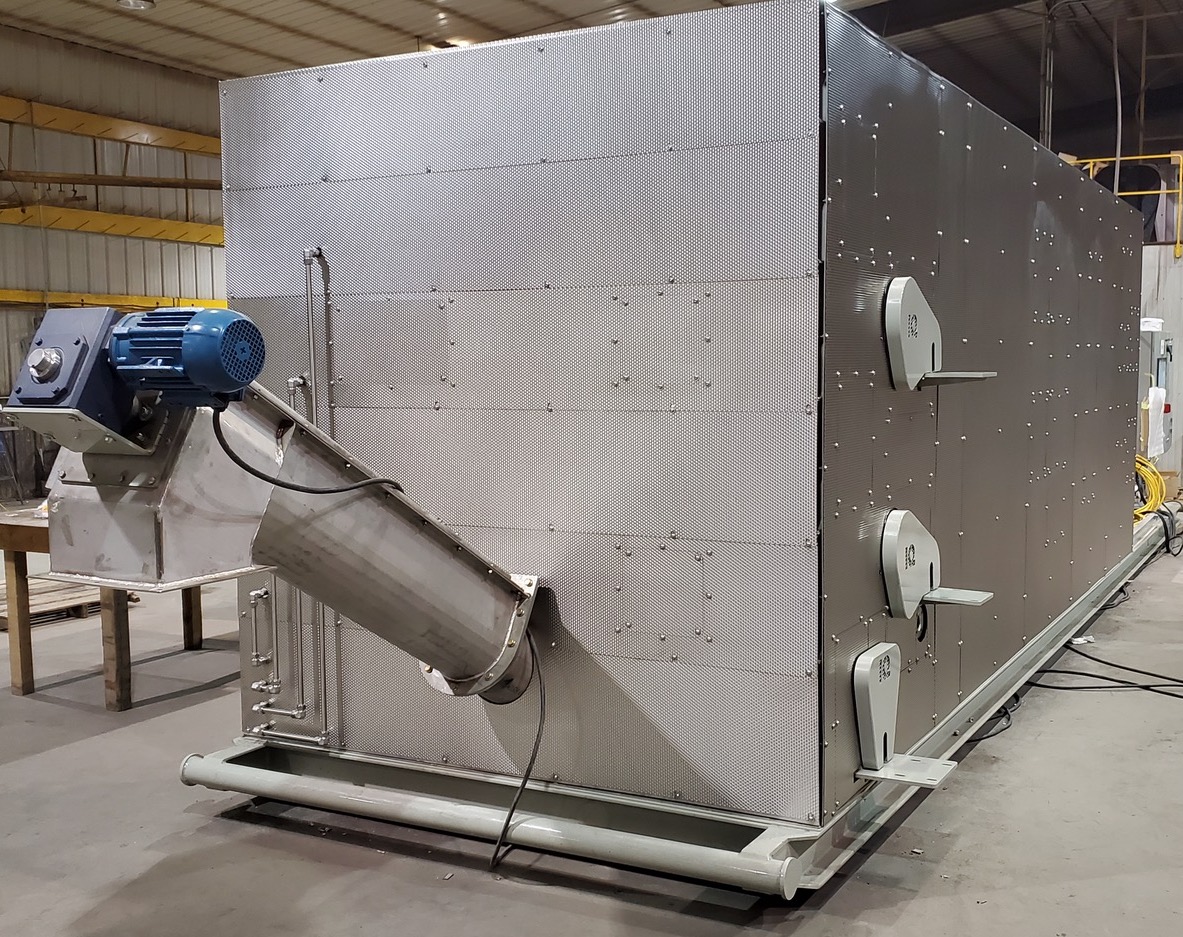
Dried Product (~15-20%mc)
Indirect Dryer Output
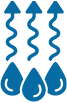
Dried Product, used for:
- Agriculture/Horticulture Use
- Industrial Use
- Carbonisation Unit Input
Residual Heat
- 80% of the heat that passed through the indirect dryer unit can be recovered for other uses
Hot Water
- Recovered water for agricultural or industrial use
Additional Benefit Examples: Carbon Credit Generation, Offset High Disposal/Trucking Costs, Offset Emissions and other additional benefits we can discuss.
IQ Energy Indirect Dryer Advantages
Highly automated, simple & effective design providing reliable, consistent plant operation
Efficient – 50% flue-gas recirculation providing for better utilisation of thermal energy.
Lower Capex – systems can be as much as 25-50% less expensive compared to other tech on the market.
Feedstocks: able to process a broad range of feedstocks from sticky and very wet materials to extremely fine and dusty materials, manures, MSW , food products, wood waste.
Modular and moveable. Ship in 40’ seacans. While also saving space with a compact footprint and low maintenance.
Exceptional accessibility and visibility into the machine and PLC control system (PLC) with user-friendly interface.
Modifiable – systems incorporate a tray design where trays can be added or removed depending on amount of material to be processed or temps of heat being used.
A Range of Heat Sources for Drying
IQ Energy’s Indirect Dryer Unit can effectively use various heat sources for the drying process.
This can include:
- Current onsite heat sources, like a cogeneration exhaust, flue gas or other onsite heat.
- Diesel or gas burners
- IQ Energy’s Carbonisation Units.
Why an Indirect Dryer Unit
no mixing of flue-gas/heat medium with the materials being dried.
Non turbulent atmosphere inside body. No dust/particulate production – eliminating back end dust controls etc.
No wet ‘stack’ or plume.
Non-diluted vapour which can be condensed with energy reused in a Boundary ORC or recirculated by employing MVR fans and exchangers.
After cooling – water can be collected and reused- not lost to the atmosphere – without need for costly heat exchangers etc.
No back-end machinery needed to deal with odour or emission to the atmosphere etc.
IQ Energy Indirect Dryer Unit Sizes
IDT1000
Smaller Indirect Dryer Unit
Processes ~8,000 wet tonnes per annum
~1 t/hour of dewatered ~20% solids (~80%mc) sludge.
IDT5000
Larger Indirect Dryer Unit
Processes ~40,000 wet tonnes/annum
~5 t/hour of dewatered ~20% solids (~80%mc) sludge
Unit Example
Commercial Indirect Dryer Unit
Alberta, Canada
- Successfully demonstrated on piggery manure.
Moving to a commercial site in Alberta in 2024 where it will dry paper mill pulp sludge commercially into the IQ Energy Carbonisation Unit. It will also be used to demonstrate biosolids, anaerobic digestate, animal wastes, and other biomass and mixed feedstocks.
Will supply dried feedstock (15-20% moisture content) to the IQ Energy Carbonisation Unit.